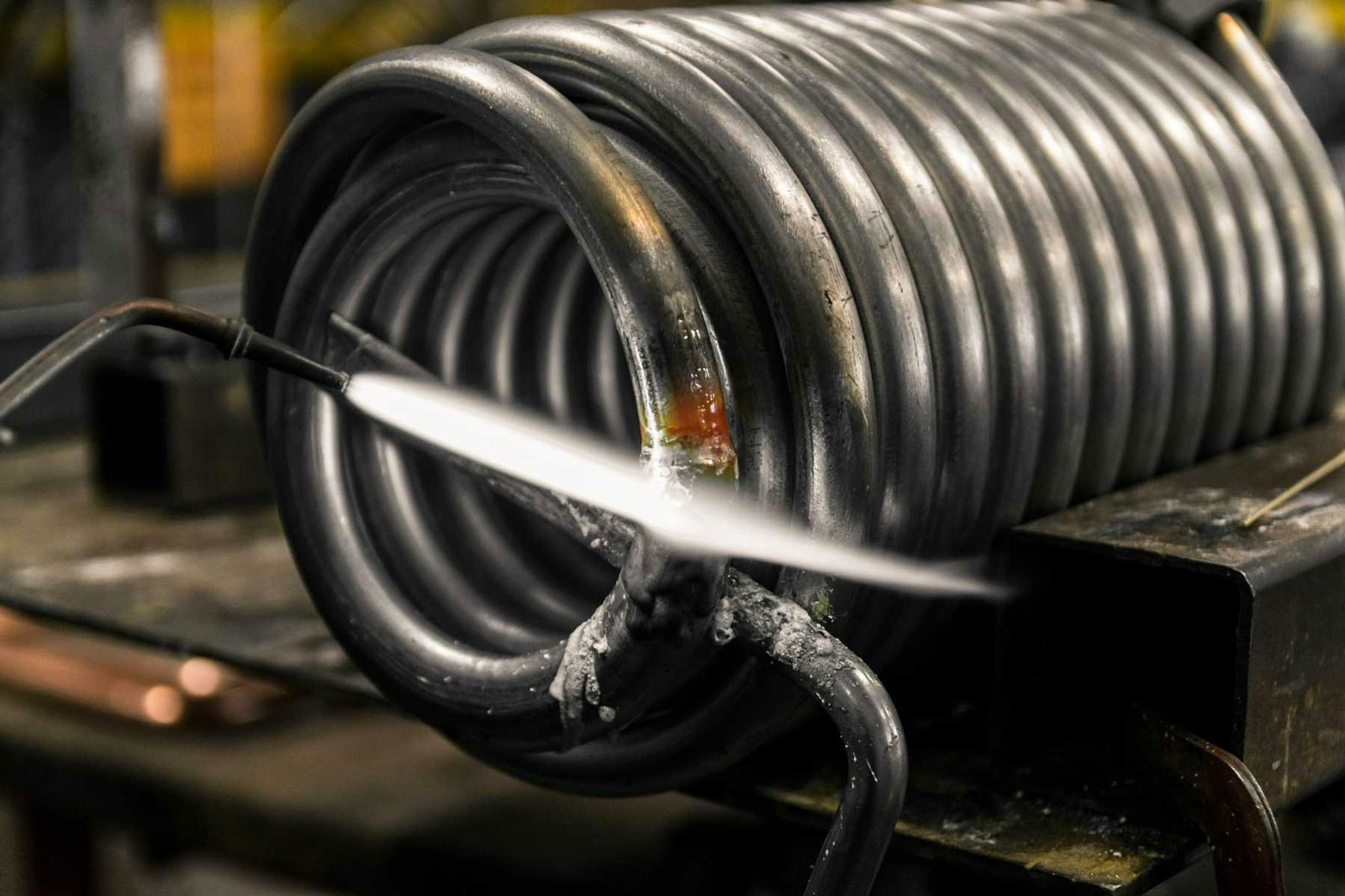
Table of Contents
- Types of Aluminum Brazing Processes
- Key Advantages of Aluminum Brazing vs. Welding
- Critical Applications in Defense and Aerospace
- Quality Considerations and Industry Standards
- The NAMF Advantage in Aluminum Brazing
- Future Trends in Aluminum Brazing Technology
- Key Takeaways
- Take Your Defense Components to the Next Level
- Frequently Asked Questions
Aluminum brazing is a specialized joining process that creates strong, leak-tight connections between aluminum components without melting the base materials. Unlike traditional welding vs. fabrication methods, brazing maintains the integrity of the original components by using a filler metal with a lower melting point that flows into the joint through capillary action.
The process typically occurs at temperatures between 1000 °F and 1200 °F (538 °C to 649 °C), well below aluminum’s melting point of approximately 1220 °F (660 °C). This critical temperature range allows the filler to flow freely while preventing any melting or deformation of the base materials.
At New Age Metal Fabricating (NAMF), one of the premier metal fabricators in NJ, we’ve specialized in aluminum dip brazing for over four decades, serving the most demanding clients in the defense and aerospace sectors. Our experience has given us unique insights into what makes this joining technology so valuable for critical applications.
Types of Aluminum Brazing Processes
Several distinct brazing methodologies exist, each with specific advantages for different applications:
- Dip Brazing: Components are immersed in a molten salt bath that serves as both heat source and flux. This method provides uniform heating and is ideal for complex assemblies with multiple joints.
- Vacuum Brazing: Performed in a vacuum furnace, this flux-free process is particularly valuable for applications requiring the highest levels of cleanliness and precision.
- Controlled Atmosphere Brazing (CAB): Conducted in a nitrogen or argon environment, CAB offers excellent control over the brazing atmosphere, reducing oxidation and contamination risks.
- Furnace Brazing: Components are heated in a furnace with controlled temperature profiles, allowing for batch processing of multiple assemblies simultaneously.
At NAMF, we’ve specialized in aluminum dip brazing, which has emerged as the preferred joining technology among top defense engineers when performance standards cannot be compromised. Our process creates metallurgical bonds that frequently exceed the base material’s inherent strength characteristics in specific loading conditions.
Key Advantages of Aluminum Brazing vs. Welding
While both welding and brazing have their place in manufacturing, several factors make brazing particularly advantageous for precision applications:
- Minimal Thermal Distortion: Unlike welding’s highly localized thermal input, dip brazing surrounds the entire assembly with a consistent temperature, eliminating the warping and distortion that frequently compromise welded aluminum structures.
- Superior Joint Quality: Brazing creates continuous, uniform joints with a surface finish. The capillary action that drives the process ensures complete joint penetration, even in complex geometries where welding access would be challenging.
- Enhanced Electrical and Thermal Conductivity: Brazed joints maintain electrical and thermal conductivity, making them ideal for components that must efficiently transfer heat or electric current.
- Join Complex and Dissimilar Materials: Brazing excels at joining dissimilar metals and complex assemblies with multiple joints. The process can simultaneously create dozens or even hundreds of joints in a single operation.
- Preservation of Material Properties: Because the base materials never reach their melting point, brazing preserves the mechanical properties and heat treatment of the original components.
- Superior Environmental Sealing: The continuous, uniform joints created through dip brazing provide superior environmental sealing and EMI shielding compared to mechanical fastening or spot welding approaches.
Critical Applications in Defense and Aerospace
The unique advantages of aluminum brazing make it particularly valuable for several specialized applications:
- Electronic Enclosures: Ruggedized housings for sensitive electronics require precise dimensional control, EMI shielding, and reliable environmental sealing. Our expertise in creating military enclosures through aluminum brazing delivers on all these requirements while providing superior thermal management.
- Radar and Communication Systems: Advanced radar and communication equipment demands housings that offer both structural integrity and precise RF characteristics. Brazed assemblies provide the necessary dimensional stability and electrical continuity.
- Thermal Management Systems: Heat exchangers, cold plates, and other thermal management components benefit from brazing’s ability to create leak-tight joints with excellent thermal conductivity.
- Structural Components: Aircraft and defense vehicle components that require high strength-to-weight ratios often utilize brazed assemblies to minimize weight while maintaining structural integrity.
- Fluid Systems: Hydraulic and pneumatic components benefit from brazing’s ability to create leak-tight joints capable of withstanding high pressures and harsh environments.
In each of these applications, the specific advantages of aluminum brazing directly address the critical performance requirements that define success in defense and aerospace environments.
Quality Considerations and Industry Standards
For defense and aerospace applications, quality standards are non-negotiable. Several key specifications govern aluminum brazing in these industries:
MIL-B-7883: This military specification establishes requirements for brazing of aluminum and aluminum alloys for defense applications, setting standards for process control, joint design, and quality assurance.
AWS C3.7/C3.7M: The American Welding Society specification for aluminum brazing provides guidelines for process qualification and quality control.
NADCAP Certification: The National Aerospace and Defense Contractors Accreditation Program certification is typically required for suppliers providing brazing services to aerospace and defense contractors.
AS9100 Certification: This quality management system standard specifically addresses the requirements of the aerospace industry.
Adherence to these standards requires rigorous process control, extensive documentation, and regular auditing. At NAMF, our quality management system is designed to meet and exceed these requirements, ensuring consistent results that meet the most demanding specifications.
The NAMF Advantage in Aluminum Brazing
With over four decades of experience in aluminum brazing for defense and aerospace applications, NAMF offers several distinct advantages:
Comprehensive In-House Capabilities
Our integrated manufacturing approach encompasses all aspects of the brazing process, from initial design consultation through final testing and certification. This single-source approach ensures consistent quality and streamlined project management. Our facilities are also equipped for brass milling and other complementary processes, making us a true one-stop shop for defense contractors.
Advanced Equipment and Facilities
Our state-of-the-art dip brazing facilities include multiple salt bath furnaces with precise temperature control and extensive monitoring capabilities. This equipment allows us to handle components ranging from small, intricate parts to large, complex assemblies. Our commitment to rapid machining technologies complements our brazing capabilities, enabling us to deliver complete solutions with efficiency.
Engineering Expertise
Our engineering team brings decades of collective experience in brazing technology, joint design, and material selection. This expertise allows us to optimize designs for brazability while meeting performance requirements. We understand the critical relationship between welding vs. fabrication techniques and can guide clients to the optimal joining solution for their specific application.
Rigorous Quality Control
Our comprehensive quality management system includes extensive in-process monitoring, non-destructive testing, and final verification to ensure consistent compliance with all applicable standards and specifications.
Industry Certifications
NAMF maintains all relevant industry certifications, including ITAR registration, ensuring our processes meet the stringent requirements of defense and aerospace applications.
Future Trends in Aluminum Brazing Technology
As we look to the future, several emerging trends are shaping the evolution of aluminum brazing technology:
Advanced Simulation and Modeling: Computational tools are increasingly being used to predict brazing outcomes, optimize joint designs, and simulate thermal profiles. These tools allow for virtual testing and refinement before physical prototyping.
Automation and Process Control: Automated handling systems and advanced process monitoring are enhancing consistency and productivity in brazing operations. Real-time feedback systems allow for immediate process adjustments to maintain optimal conditions.
New Filler Metal Formulations: Ongoing research into brazing filler metals is yielding new formulations with improved flow characteristics, reduced brazing temperatures, and enhanced mechanical properties.
Sustainability Considerations: Environmental factors are driving innovations in flux formulations, energy efficiency, and waste reduction throughout the brazing process.
At NAMF, we continuously monitor these developments and integrate new technologies and approaches that enhance our capabilities and the value we deliver to our clients.
Key Takeaways
- Aluminum brazing creates superior metallurgical bonds without the thermal distortion issues common in welding, making it ideal for precision defense components.
- NAMF provides specialized dip brazing services along with brass milling and rapid machining capabilities as one of the leading metal fabricators in NJ.
- Military enclosures and electronic housings benefit most from aluminum brazing due to superior EMI shielding and environmental sealing properties.
Take Your Defense Components to the Next Level
Ready to experience the superior quality and performance that only professional aluminum brazing can deliver? Our team of experts is ready to discuss your specific requirements and demonstrate how our brazing expertise can enhance your defense or aerospace components.