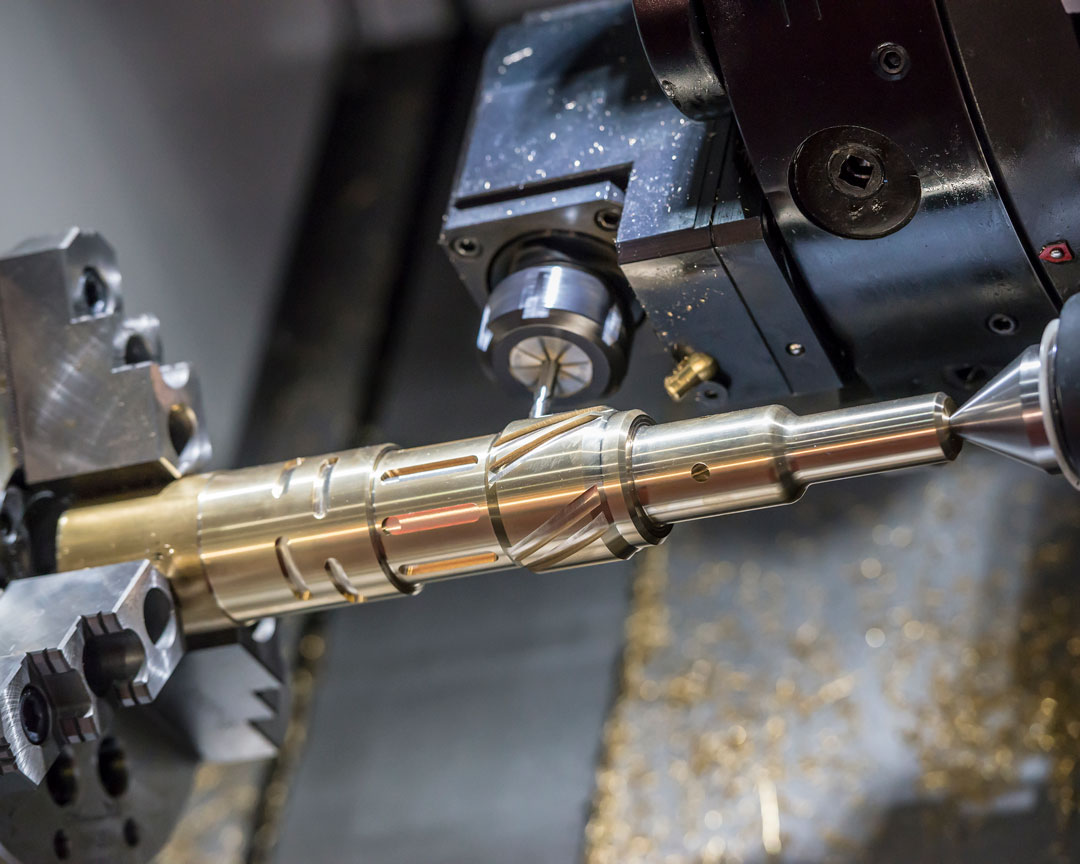
Table of Contents
When it comes to critical custom parts for the defense or aerospace industries, there can be no room for error. To create the high-precision parts needed, brass milling combines the accuracy of computer numerical controlled (CNC) milling machines, with the unique qualities of brass.
Together, they create parts that meet the strict requirements of high-demand environments. If you’re interested in knowing more about the process of brass milling, read on for a quick overview of what it’s all about.
What Is Brass Milling?
Precision brass milling is a machining process that enables the production of precisely formed components. Rotary cutters remove material by being pressed into a workpiece using a CNC milling machine that performs many, small cuts to shave chips off the workpiece. The two major classes of milling are:
- Face milling: Used to cut flat-bottomed cavities, or flat surfaces, into a workpiece
- Peripheral milling: The cutter blades scoop material out from the workpiece to create deep slots, threads, or gear teeth
Milling machines use the processes such as drilling, boring, and grooving to manufacture parts with various finishes, as desired.
Three Factors That Define Brass Milling
There are three factors that set brass milling apart from other manufacturing processes:
1. Clamping
As the router rotates at 5000-6000 rpm, tremendous force exerts on the workpiece from the top down and sideways, which makes clamping it from the top and sides is essential. The baseplate can be made of polycarbonate or metal.
Dowel pins, normally made from steel, clamp the workpiece down. The dowel pins slot into the baseplate and hold the workpiece in place. The clamps and baseplate are water-resistant, as the CNC milling process usually requires a spray of coolant to prevent a meltdown as the process generates heat.
2. End Mills
The rotational power in CNC Milling comes from the router, while the brass is cut using end mills coated in carbide. There are three basic types of end mills:
- Flat end mills are best for clearing away material
- A round nose mill is ideal for smooth finishing passes
- V-Type is used for engraving into non-ferrous alloys, such as brass.
The bits are available in different flute counts, single, double, and four-flute. The flute is the cutting edge of the mill that shears off the material when spinning at high speed. The single flute is usually used for brass as it removes the sheared metal quickly and doesn’t give the brass a chance to melt and cause clogging, which could happen with higher flute counts.
3. Feed Rate and Plunge Cut
Feed rate is the speed that the router takes to get from one point to the other. Slower speeds allow for better milling, but slow speeds make the process of milling take longer.
This costs both energy and production time. Finding the right balance for each project is key.
Plunge depth refers to how deep the end mill goes into the metal at each pass and is measured in millimeters. While wood milling can cut up to 4 mm deep with each pass, brass can be removed at approximately 0.15 mm at a time to prevent breaking the end mill.
Horizontal vs. Vertical Milling
Different types of milling machines are used for different applications. The most common two categories of milling machines or vertical and horizontal.
The two types of machines complement each other and provide outstanding flexibility to the manufacturing process. These are the factors that influence which machine is best for the application:
- Cut accuracy: For precision brass milling where greater accuracy is required, vertical machining centers give a better result
- Material removal rate: Horizontal machining allows bigger cuts at a similar cutting tool speed
- The number of sides requiring machining: Vertical milling machines are better suited to a single plane, while horizontal milling machines work well for multiple sides needing to be machined at various angles
- Customization required: Both milling machines can work with various tools, but the horizontal milling machine allows for much greater customization
In summary, the horizontal milling machine is far more versatile than its vertical counterpart.
Why Is Brass Good for Machining?
Brass is a zinc-copper alloy that is a versatile metal. It offers a highly durable end product. Here are some other factors that make it an ideal choice for milling.
High-Speed Machining
As the mechanical properties of brass are high strength, shear resistance, and high tensile strength, brass offers excellent machinability. All these factors enable brass to be machined at high speed, five to twenty percent higher than other CNC machining processes.
Precision Machining and Stability
Brass displays excellent dimensional stability, making it suitable for strict tolerance manufacturing. The dimensional stability of brass is due to its high-impact resistance and lower deformation factor. This makes it an ideal material for prototyping new designs.
High Tool Compatibility
Brass offers friction-free machining and negligible chip formation, which reduces tool wear and tear. Brass rod workpieces are usually preferred for CNC milling as they are compatible with various machining tools.
Material Grade Variety
Brass is available in different grades that have different applications. These are two of the main grades of brass available:
- Brass C35300 grade: Offers higher immunity against wear and tear, less operational friction, and corrosion resistance
- Brass C36000 grade: With superior machinability, this grade is for producing intricate parts that demand precise dimensional manufacturing
Higher Production Levels and Profitability
As brass CNC machining is a fast, precise process, it increases the efficiency of the process, which leads to higher production levels. Repair, maintenance, and tool replacement costs are relatively low, and tool durability in the brass milling process is high.
Post-machining treatments aren’t needed with brass milling. All these factors contribute to increased productivity and higher profit margins.
Eco-friendly Operation
The brass used in brass milling is a copper alloy that remains similar to natural copper in terms of chemical properties, which makes it an eco-friendly material to work with. Brass CNC machining doesn’t emit chemicals or harmful gases into the atmosphere. Brass milling is a zero scrap process as all the excess materials and shaving are 100% recyclable, making it an eco-friendly process.
The Role of Brass Milling in a Manufacturing Process
Brass milling offers components that are useful across all different industries and applications because of their precise design and the benefits that brass offers.
Key Takeaways:
- Brass milling delivers exceptional precision and high-speed machining capabilities essential for critical applications like military enclosures and defense components, offering superior dimensional stability and tight tolerances.
- CNC brass milling provides eco-friendly, zero-scrap manufacturing with 100% recyclable materials and reduced tool wear, making it more cost-effective than traditional processes used by many metal fabrication companies.
- Brass’s excellent machinability and tool compatibility enable faster production rates and higher profitability for military fabrication projects requiring complex geometries and precise specifications.
Precision Brass Milling for Your Critical Applications
Transform your manufacturing capabilities with our advanced brass milling services. From military-grade components to precision prototypes, we deliver the accuracy and reliability your projects demand.