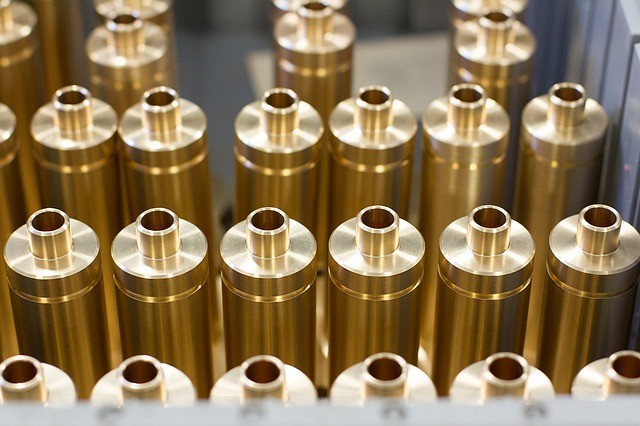
Table of Contents
Chem Film Coating
There is an inexpensive, easy way to extend the life of metal products and surfaces, adding durability and longevity. Chemical film coating, sometimes known as chem film, is a sealant and finishing technique that ensures both long lasting quality, and metal product safety.
What is Chemical Film Coating and How Does it Work?
Chemical film coating works by applying a chemical like chromate to a metal substrate. Metals including steel, aluminum, zinc, cadmium, copper, silver, magnesium, and tin alloys are all suitable for this type of finishing process. The process forces a reaction between the metal and the chemical conversion materials.
It usually begins with an acid or agitation cleaning to ensure that the metal product is clean of any dirt, oil, or residues, then rinsed and dried. The metal is then immersed in the chem film coating solution. It can also be applied through a spraying or brushing technique. It’s rinsed again when the chemical film coating is finished applying.
Chem film coating works through adhering in a thin film to the metal surface or product, acting as a sealant to protect the underlying material. The coatings are categorized into types and classes.
Type I coating is usually brown or gold in color, also available as a clear coating. It includes chemical film compositions that contain hexavalent chromium. Type II coating contains no hexavalent chromium and is usually colorless. Class 1A provides corrosion prevention for unpainted items, and also makes it easier for paint finish to adhere if the product is set to be painted. Class 3 is generally used for electrical or electronic applications destined for lower resistance contacts, as the coatings are thinner. They do prevent corrosion but not as well as Class 1A coatings, and Class 3 coatings can also be used to improve paint adhesion.
The appropriate type and class of chem film coating depend on the product and its use.
Benefits of Chemical Film Coating
Chem film coating offers many benefits, all of which work to ensure metal product safety.
First, this type of finishing technique offers protection against corrosion without increasing the size of the part that is being coated. It is a very efficient, cost-effective way to keep your budget in check while ensuring product quality, safety and durability.
With chem film coating in place, products will not interfere with electrical impedance. For any electrical applications chemical film coating is ideal because it will not alter the electrical conductivity of the part.
Aerospace and Film Coating
Product safety is vital in any industry, aerospace included, which is why chemical film coating has a big role to play.
In the aerospace industry, chemical film coating is often used for anodized surface repair, and to ensure that all applicable parts are protected from corrosion, a common issue given that these vehicles operate at high speed and high altitudes, exposed to many elements. Corrosion isn’t just ugly, it can seriously alter the integrity of a part, which is unacceptable in aviation. Atmospheric corrosion is a major concern in the aerospace industry and something that cannot be avoided, but it can be mitigated through processes like chem film coating.
Film coating, much like it does not add to the size of a part, will not add to the weight either, which is important for the aerospace industry as weight is carefully calibrated down to the ounce.
There is no room for error in the reliability and quality of parts destined for the aerospace industry, something we fully understand and take very seriously. As with all that we do, our chemical film coating work is done to the highest standards. New Age Metal Fabricating is approved by the National Aerospace and Defense Contractors Accreditation Program for chemical conversion coating, offering Type I, classes 1A and 3, and Type II, classes 1A and 3 to suit your needs.
All of our metal fabrication and metal machining services work is done in-house, as a single source supplier of the parts and products you need. There’s no need to bounce from supplier to supplier, as we control each step of the manufacturing process at our facilities, including chem film conversion. The end result is a well made, durable product, handled completely by the experienced staff at the New Age companies. You can rely on us to supply you with everything you need, connecting you to our business through a single dedicated point of contact.
We are happy to answer any questions you may have about chemical film conversion, or provide you with a quote for your own product or part needs. Get in touch with us today! [cta txt=”Contact Us Today!”]